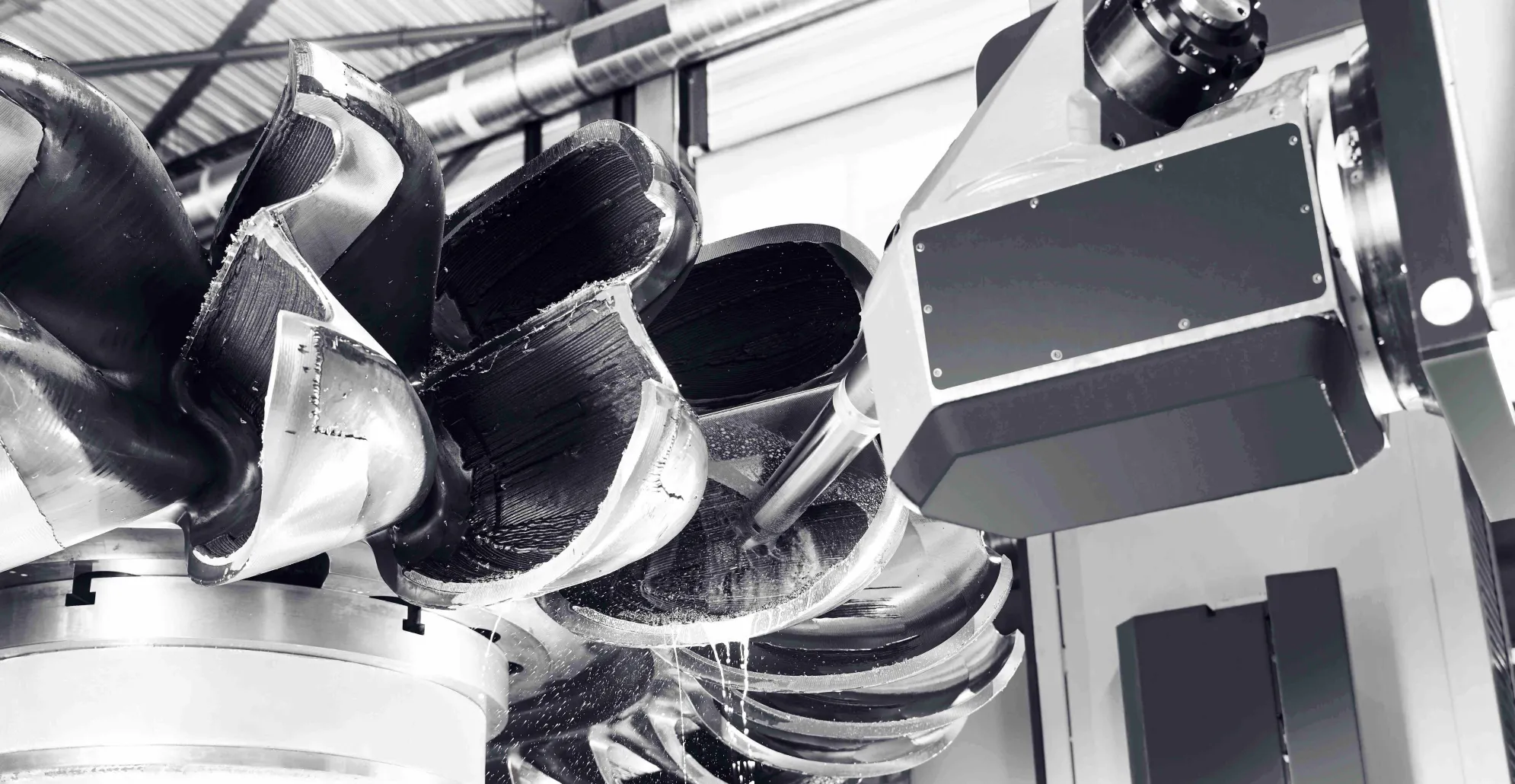
Refurbishing Pelton turbine wheels on an MTE.
In the context of the energy transition, hydropower plants, especially pumped storage power plants, are becoming increasingly important as they offer a reliable and flexible storage solution to effectively balance fluctuating energy demand from renewable sources. The maintenance of hydropower plants plays a crucial role in ensuring efficient energy production in the long term.Even Pelton turbine wheels need to go to the workshop sometimes. This one has a diameter of 2,762 mm and weighs 7,554 kg. As part of a hydroelectric turbine at our customer Kraftwerke Oberhasli (KWO), it drives a generator to produce electricity. Due to wear and tear, the "Pelton cups" had to be repaired after 21,000 operating hours. This means shutting down the turbine, dismantling the wheel and re-welding pockets wherever there is severe abrasion or holes. At KWO, this was done by a welding robot. And now our FBF-M 4000 floor type milling machine comes into play. It is used to mill each cup back to its original dimensions and shape with high precision.
At speeds of up to 3,500 rpm, the water injected by the nozzle must flow perfectly at a pressure of 81 bar. This is the only way to avoid turbulence and achieve high efficiency, thereby ensuring efficient energy yield.
But there are even greater challenges to overcome. At KWO, for example, a Pelton wheel with an impressive diameter of 3,612 mm and a weight of 17,500 kg is in operation. Even this giant wheel could be successfully machined on our FBF-M 4000 floor type milling machine, which underlines the versatility and performance of this state-of-the-art floor type milling machine. In the world of hydropower, innovation and precision are key factors contributing to the efficiency and longevity of the plants.